Missouri Meerschaum Factory Tour: Difference between revisions
(Created page with "The following photos are from a factory tour on my visit in March of 2019. Several of the pipe makers have worked for Missouri Meerschaum for thirty years. The ones I spoke wi...") |
No edit summary |
||
Line 1: | Line 1: | ||
The following photos are from a factory tour on my visit in March of 2019. Several of the pipe makers have worked for Missouri Meerschaum for thirty years. The | [[File:MissouriMeerschaum-Building.jpg|thumb|350px|The factory as it stands in March 2019, when visited by [[S.E. Thile Pipes|Scott Thile]], Pipedia founder, and avid smoker of cobs]]The following photos and narrative are from a factory tour on my visit in March of 2019. The wonderful old building is just across the road from the Missouri River, which can be seen out wonderful old windows that originally supplied the light to work by. The corner section is the original building, which was added onto in various stages, both upstairs and upriver, to keep up with the growing demand for cobs in the early to middle 20th century. [[Henry Tibbe]] made the early pipes using a foot powered trundle lathe and other hand tools in a much smaller workshop, and resisted the notion of scaling up as demand increased. | ||
Henry's son, Antone Tibbe is responsible for the building and additions, and was the primary force in the scaling up of the company. Most of third floor is now used for housing an inventory of cobs (aged at least 2 years before being crafted into pipes). There is also ample storage for some older machines, which are often gleaned for parts to maintain the machines that are still in production. The second floor has more cobs in storage, as well office space, and a wonderful museum and gift shop. The making of pipes, packaging, and shipping and receiving are on the first floor. There is an old freight elevator facilitating the production. It is driven by the original belt and cable system which was first power by steam, and later converted to electricity. It is still carefully controlled using the same antiquated system. A false move can mean the un-spooling of a large cable. Thankfully that is rare! | |||
Most of the older machines still in production were designed and built by a nearby machine shop that is owned and operated by the same family today as had originally built them. And they still maintain them. Some the machines date back to when the factory was powered by steam when Anton Tibbe, the founder's son and successor needed power to meet the growing demand. Antone later brought electric power to Washington in order to keep the machinery churning out cobs. There is an old Tibbe Power Company building standing just to the north of the factory. | |||
At the time of my visit the company had a total of 35 employees, 5 were in the office, 2 are full time with growing, harvesting, and shelling the corn cobs across the Missouri river from the factory (I hope to visit that part of the operation at some point), and the other 28 or so employees were working on various stages of making the pipes. | |||
Several of the pipe makers pictured in the photos have worked for Missouri Meerschaum for thirty years, others are younger, and learning the ropes. The workers I spoke with took a great deal of pride in their work and being part of an American tradition that is enjoyed Worldwide. | |||
One of the great appeals of the Missouri Meerschaum Company is the tradition, another is the vertical integration. Even the grain is used, though not by Missouri Meerschaum. Some of it is sold to company making whiskey. Some of the cobs are now being made into duck calls by a local Washington Missouri woodworker. | |||
<gallery widths=300 heights=200 caption="Factory Tour, March 2019"> | <gallery widths=300 heights=200 caption="Factory Tour, March 2019"> | ||
File:MissouriMeerschaum-Stacks.jpg|One of many stacks of cobs aging (a minimum of two years before being made into pipes) | File:MissouriMeerschaum-Stacks.jpg|One of many stacks of cobs aging (a minimum of two years before being made into pipes) | ||
File:MissouriMeerschaum-cobs.jpg|Corn cobs awaiting their fate | File:MissouriMeerschaum-cobs.jpg|Corn cobs awaiting their fate | ||
Line 11: | Line 19: | ||
File:MissouriMeerschaum-after-drilling-chamber2.jpg|Cobs after drilling chamber | File:MissouriMeerschaum-after-drilling-chamber2.jpg|Cobs after drilling chamber | ||
File:MissouriMeerschaum-after-drilling-chamber.jpg|Cobs after drilling chamber | File:MissouriMeerschaum-after-drilling-chamber.jpg|Cobs after drilling chamber | ||
File:MissouriMeerschaum-plugged.jpg|Cobs after plugging with maple | |||
File:MissouriMeerschaum-drilled&ready4shaping.jpg|Cobs waiting to be shaped | File:MissouriMeerschaum-drilled&ready4shaping.jpg|Cobs waiting to be shaped | ||
File:MissouriMeerschaum-shaping-machine1.jpg|One of several fraising (shaping) machines used for some of the standard shapes | File:MissouriMeerschaum-shaping-machine1.jpg|One of several fraising (shaping) machines used for some of the standard shapes | ||
File:MissouriMeerschaum-shaping-machine3.jpg|Another fraising machine, with cobs ready to place on spindles in the foreground, and shaped cobs come off the spindals and into a metal drawer on the floor | |||
File:MissouriMeerschaum-shaping-machine2.jpg|Cobs heading into the fraising machine | File:MissouriMeerschaum-shaping-machine2.jpg|Cobs heading into the fraising machine | ||
File:MissouriMeerschaum-shaping-machine.jpg|Operating the fraising machine | File:MissouriMeerschaum-shaping-machine.jpg|Operating the fraising machine | ||
Line 18: | Line 28: | ||
File:MissouriMeerschaum-lathe.jpg|Many of the shapes are hand turned on one of several lathes | File:MissouriMeerschaum-lathe.jpg|Many of the shapes are hand turned on one of several lathes | ||
File:MissouriMeerschaum-lathe2.jpg|Lathe work | File:MissouriMeerschaum-lathe2.jpg|Lathe work | ||
File:MissouriMeerschaum-plugging1.jpg|Some of the models have maple plugs glued into bottoms, others do not require one. Here the craftsman is gluing applying glue in preparation for the plug | |||
File:MissouriMeerschaum-sanding.jpg|Sanding the outside of the bowls to smooth and carefully refine the shape | File:MissouriMeerschaum-sanding.jpg|Sanding the outside of the bowls to smooth and carefully refine the shape | ||
File:MissouriMeerschaum-sanding2.jpg|Sanding work | File:MissouriMeerschaum-sanding2.jpg|Sanding work | ||
File:MissouriMeerschaum-mixing-plaster.jpg|Mixing | File:MissouriMeerschaum-mixing-plaster.jpg|Mixing plaster of Paris. This treatment was developed by Henry Tibbe, the founder of Missouri Meerschaum. Henry found the plaster of Paris process gave the cobs a character similar to Turkish Meerschaum, hence the inspiration for naming his company. | ||
File:MissouriMeerschaum-plastering.jpg|All done by feel--feel of plaster consistency, feel | File:MissouriMeerschaum-pouring-cobs.jpg | ||
File:MissouriMeerschaum-plastering3.jpg|Inspecting the next cob to have plaster applied | File:MissouriMeerschaum-plastering.jpg|All done by feel--feel of plaster consistency, feel for the amount used, and feel of when it has been worked optimally into the cob | ||
File:MissouriMeerschaum-plastering3.jpg|Inspecting the next cob bowl to have plaster applied | |||
File:MissouriMeerschaum-plastering2.jpg|Plastering detail | File:MissouriMeerschaum-plastering2.jpg|Plastering detail | ||
File:MissouriMeerschaum-plastered-bowls.jpg|Bowls drying after plastering (takes a day or so before they can be sanded) | File:MissouriMeerschaum-plastered-bowls.jpg|Bowls drying after plastering (takes a day or so before they can be sanded again) | ||
</gallery> | </gallery> | ||
Revision as of 00:14, 25 March 2019
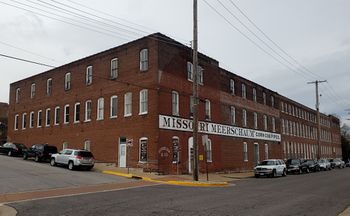
The following photos and narrative are from a factory tour on my visit in March of 2019. The wonderful old building is just across the road from the Missouri River, which can be seen out wonderful old windows that originally supplied the light to work by. The corner section is the original building, which was added onto in various stages, both upstairs and upriver, to keep up with the growing demand for cobs in the early to middle 20th century. Henry Tibbe made the early pipes using a foot powered trundle lathe and other hand tools in a much smaller workshop, and resisted the notion of scaling up as demand increased.
Henry's son, Antone Tibbe is responsible for the building and additions, and was the primary force in the scaling up of the company. Most of third floor is now used for housing an inventory of cobs (aged at least 2 years before being crafted into pipes). There is also ample storage for some older machines, which are often gleaned for parts to maintain the machines that are still in production. The second floor has more cobs in storage, as well office space, and a wonderful museum and gift shop. The making of pipes, packaging, and shipping and receiving are on the first floor. There is an old freight elevator facilitating the production. It is driven by the original belt and cable system which was first power by steam, and later converted to electricity. It is still carefully controlled using the same antiquated system. A false move can mean the un-spooling of a large cable. Thankfully that is rare!
Most of the older machines still in production were designed and built by a nearby machine shop that is owned and operated by the same family today as had originally built them. And they still maintain them. Some the machines date back to when the factory was powered by steam when Anton Tibbe, the founder's son and successor needed power to meet the growing demand. Antone later brought electric power to Washington in order to keep the machinery churning out cobs. There is an old Tibbe Power Company building standing just to the north of the factory.
At the time of my visit the company had a total of 35 employees, 5 were in the office, 2 are full time with growing, harvesting, and shelling the corn cobs across the Missouri river from the factory (I hope to visit that part of the operation at some point), and the other 28 or so employees were working on various stages of making the pipes.
Several of the pipe makers pictured in the photos have worked for Missouri Meerschaum for thirty years, others are younger, and learning the ropes. The workers I spoke with took a great deal of pride in their work and being part of an American tradition that is enjoyed Worldwide. One of the great appeals of the Missouri Meerschaum Company is the tradition, another is the vertical integration. Even the grain is used, though not by Missouri Meerschaum. Some of it is sold to company making whiskey. Some of the cobs are now being made into duck calls by a local Washington Missouri woodworker.
- Factory Tour, March 2019
Stay tuned, more photos are coming...